GENERAL INTRODUCTION
The AAC production process includes raw material preparation, batching and mixing, pouring, pre-curing, cutting, autoclaving, and packing.
With decades of experience in serving the AAC blocks production machinery industry, we can supply customers with quality AAC block production lines with capacity ranging from 150,000m3 to 40,000m3 per year.
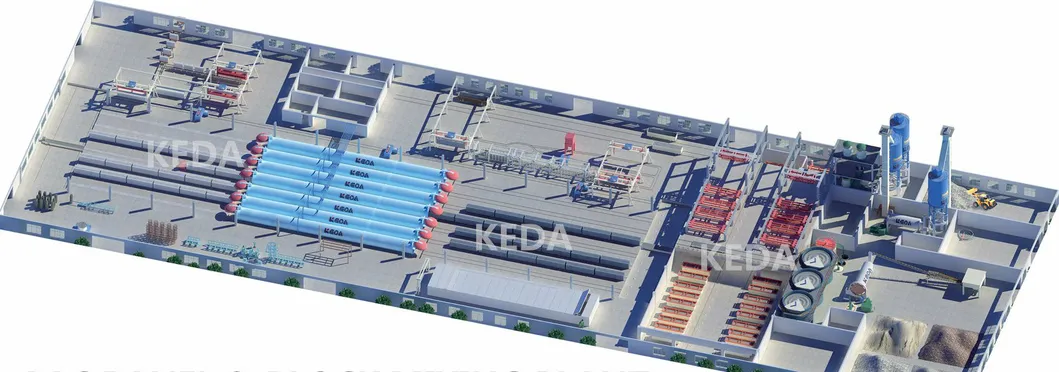
AAC BLOCK / BRICK / PANEL MAKING MATERIAL
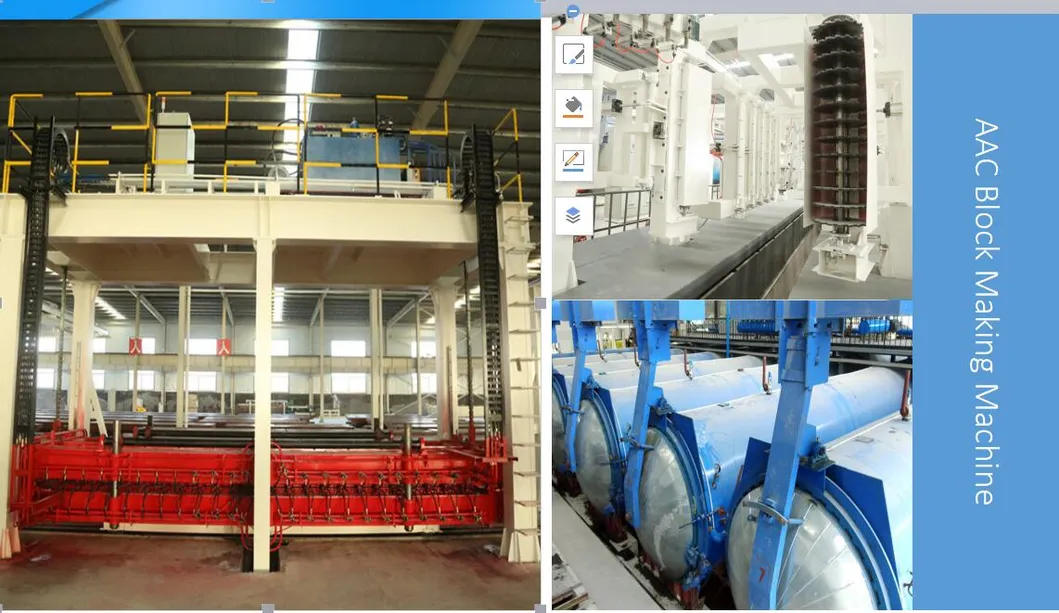
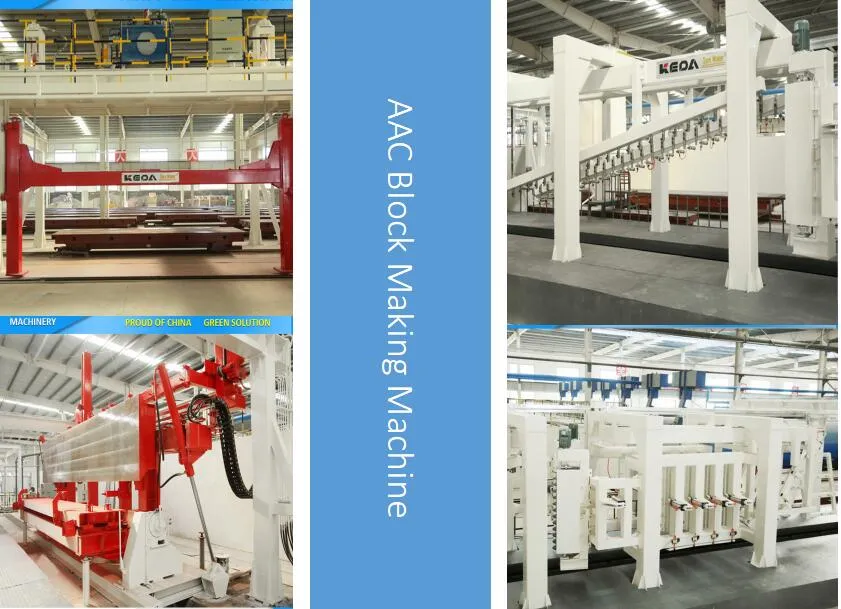
AAC FINAL PRODUCTS ADVANTAGES
AAC is a high-tech product that protects the environment and is used in a wide range of industries such as public works, industrial construction, civil housing, hospitals, hotels and schools. It can also be used in the building structure as external panels, floor panels and roof slabs.
AAC products have special characteristics such as:
Thermal Insulation:When used to build external walls, AAC products meet all strict requirements made by various countries without use of any other auxiliary thermal protecting materials. Tests show that AAC products with a thickness of 4-5cm perform the same function of thermal protection as one layer of common blocks; with a thickness of 7-8cm. AAC provides the same level of thermal protection as bricks double the thickness. Therefore AAC is not only a material that can be used to structures, it is also a high quality thermal material.
Accuracy:AAC manufacturing technology and sophisticated equipment ensure dimensional accuracy with discrepancies within 1.0 mm on each face. Such performances outperform the national standard requirement.
High Load Capacity:Because AAC products are cut on six faces with accuracy and installed by the use of a very thin layer of Mortar; this results in a high-strength product with hardness.
Convenient Construction:AAC products can be sawn, drilled, nailed and machined using normal wood working tools. Also, simple construction details allow the designer, detailer and contractor to quickly and confidently complete the project without any anxiety over difficulty or voluminous details.
Moisture Resistance:The cellular structure of AAC products are comprised of many independent, tiny and dispersed air spaces. Such a unique structure enables AAC products to effectively prevent water from penetrating through it.
Fire resistance:The raw materials used in AAC products are absolutely non-combustible. Experiment results show that 10-cm thick walls made of AAC could stand against fire for at least 4 hours.
Sound Insulation:Test results shows that AAC products have excellent acoustic performance. Walls made of AAC could reduce the noise range from 30-52dB depending on the thickness of the walls and different surface disposed.
Reduce the Cost:Costs can be greatly reduced due to the lower input on construction and better site management. As the product is environmentally friendly, very little cleaning work is required.
Green Design:AAC product is by no means harmful to the environment. All the materials are completely natural.
AAC BLOCK PRODUCTION PROCESS
Mixing period 5-6 minutes
Pouring slurry temperature 40-45ºC
Cake curing time 2.5-3.0h
Cake curing temperature 45~55ºC
Cake strength after curing 0.15~0.18MPa
Autoclaved curing system
Before-after autoclave 0.5h
Vacuumize 0.5h(0~-0.06MPa)
Listing pressure 1.5h(-0.06~1.3MPa)
Constant pressure 8h(1.3MPa)
Releasing pressure 1.5h(1.3~0MPa)
total 12h
CUTTING SYSTEM
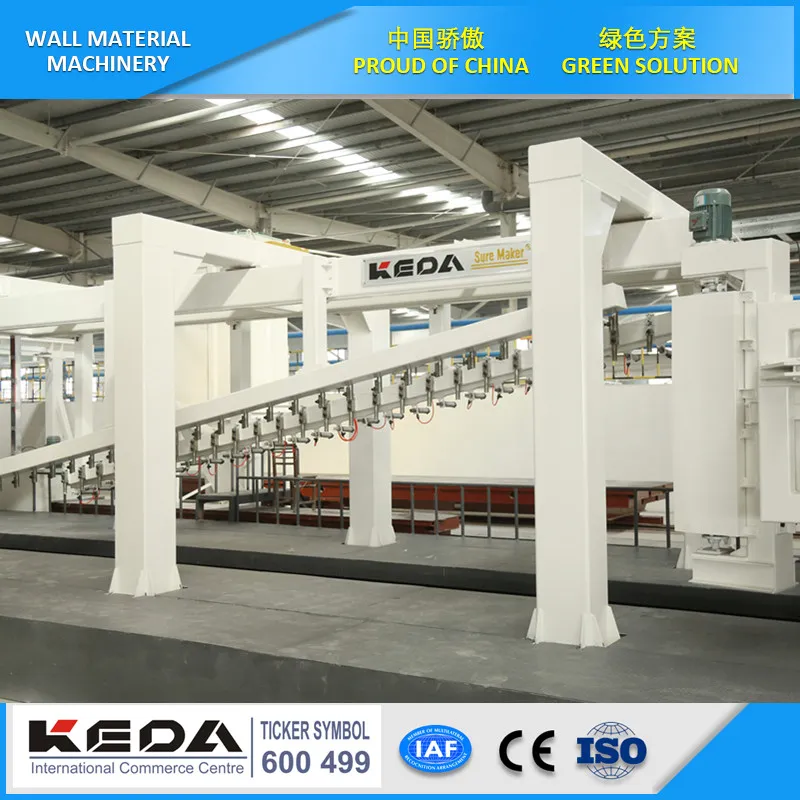
![]() | |
All the steel wire posts are fixed on two main oblique beams and each pair of posts is used to fix only one steel wire, so that the horizontal cutting machine can solve the settlement cracks problem in thin block and panel cutting, and achieve the minimum horizontal cutting thickness of 50MM block out of a whole mould. | |
The stability and accuracy of the vertical cutting machine can both reach the international advanced level. The integral swing frame can ensure the side plate replacement, the cutting can be synchronized with ferry replacement. With the automatic detection system, the broken wire can be timely detected. |
AAC FINAL PRODUCTS
1.Product classificationProduct classification is according to national standards GB/T 11968-2006 AAC block, also can be according to user's requirements to produce product with special specifications size.
Chart 1 Specification & Index
Name | AAC block |
Weight | 300~600 Kg/m3(control led by formula) |
After autoclave compressive strength | average value≥3.5MPa, Min. value<=2.8Mpa |
Drying shrinkage value | Measured under condition of rapid method≤0.8mm/m;Measured under condition of standard method≤0.5mm/m |
Frost-resistance | After the cycle of freezing and thawing for 15 times,weight loss≤ 5%,strength loss≤ 20% |
Coefficient of thermal conductivity | ≤0.14~0.16W/m.k |
1.2 The block is classified by compressive strength and volume density.
Strength level: A1.0, A2.0, A2.5, A3.5, A5.0, A7.5, A10.
Dry density level: B03, B04, B05, B06, B07, B08.
1.3 Block level
The block is divided into high-class(A), first-class(B), qualified product (C) according to the size variation, appearance quality, dry density, compression strength & frost-resistance.
1.4 AAC Block indicator
Chart 3 Size variation& appearance
Project | Indicator | |||
High-class (A) | Qualified product (B) | |||
Permissible variation of dimension mm | Length | L | ±3 | ±4 |
Width | B | ±1 | ±2 | |
Height | H | ±1 | ±2 | |
Missing angle | The min. size not more than /mm | 0 | 30 | |
The max. size not more than /mm | 0 | 70 | ||
Missing angle no. larger than the above size, not more than | 0 | 2 | ||
Crack length | The crack length through one edge and two surfaces not more than crack directional size sum on crack surface | 0 | 1/3 | |
The crack length of any surface can not be larger than crack directional size | 0 | 1/2 | ||
The cracks larger than the above size, not more than | 0 | 30 | ||
The depth of cracking, sticking, damage can not be more than/mm | 0 | 1030 | ||
Plain bending | Not allowed | |||
Surface porosity, lamination crack | Not allowed | |||
Surface oil | Not allowed |
Chart 4 Cubic compression strength for block
Strength level | Cubic compression strength (MPa) | |
Average not less than | Single group min. not less than | |
A1.0 | 1.0 | 0.8 |
A2.0 | 2.0 | 1.6 |
A2.5 | 2.5 | 2.0 |
A3.5 | 3.5 | 2.8 |
A5.0 | 5 | 4.0 |
A7.5 | 7.5 | 6.0 |
A10.0 | 10 | 8.0 |
Chart 5 Dry density for block(kg/m3)
Dry density level | B03 | B04 | B05 | B06 | B07 | B08 | |
Dry density | High-class (A)≤ | 300 | 400 | 500 | 600 | 700 | 800 |
Qualified product (B)≤ | 325 | 425 | 525 | 625 | 725 | 825 |
Chart 6 Strength level for block
Dry density level | B03 | B04 | B05 | B06 | B07 | B08 | |
Strength level | High-class (A)≤ | A1.0 | A2.0 | A3.5 | A5.0 | A7.5 | A10.0 |
Qualified product (B)≤ | A2.5 | A3.5 | A5.0 | A7.5 |